- % SALE %
- Temperature
- Humidity
- Pressure
- Light Intensity & Motion
- Air Quality & Flow
- Modbus | Wireless Modbus
- PowerIO®
- EtherCAT P
- Accessory
Differential pressure transducers:
Accurate measurement for building automation
Welcome to our comprehensive guide on differential pressure transducers for building automation.
These advanced sensors accurately measure the pressure difference between two points, typically referred to as P1 and P2 or high side (HI) and low side (LO). Differential pressure transducers can be used to measure fluid or gasses. They find applications in various industries. Prime examples are monitoring level in a (sealed) tank, filter cleanness or flow measurement.
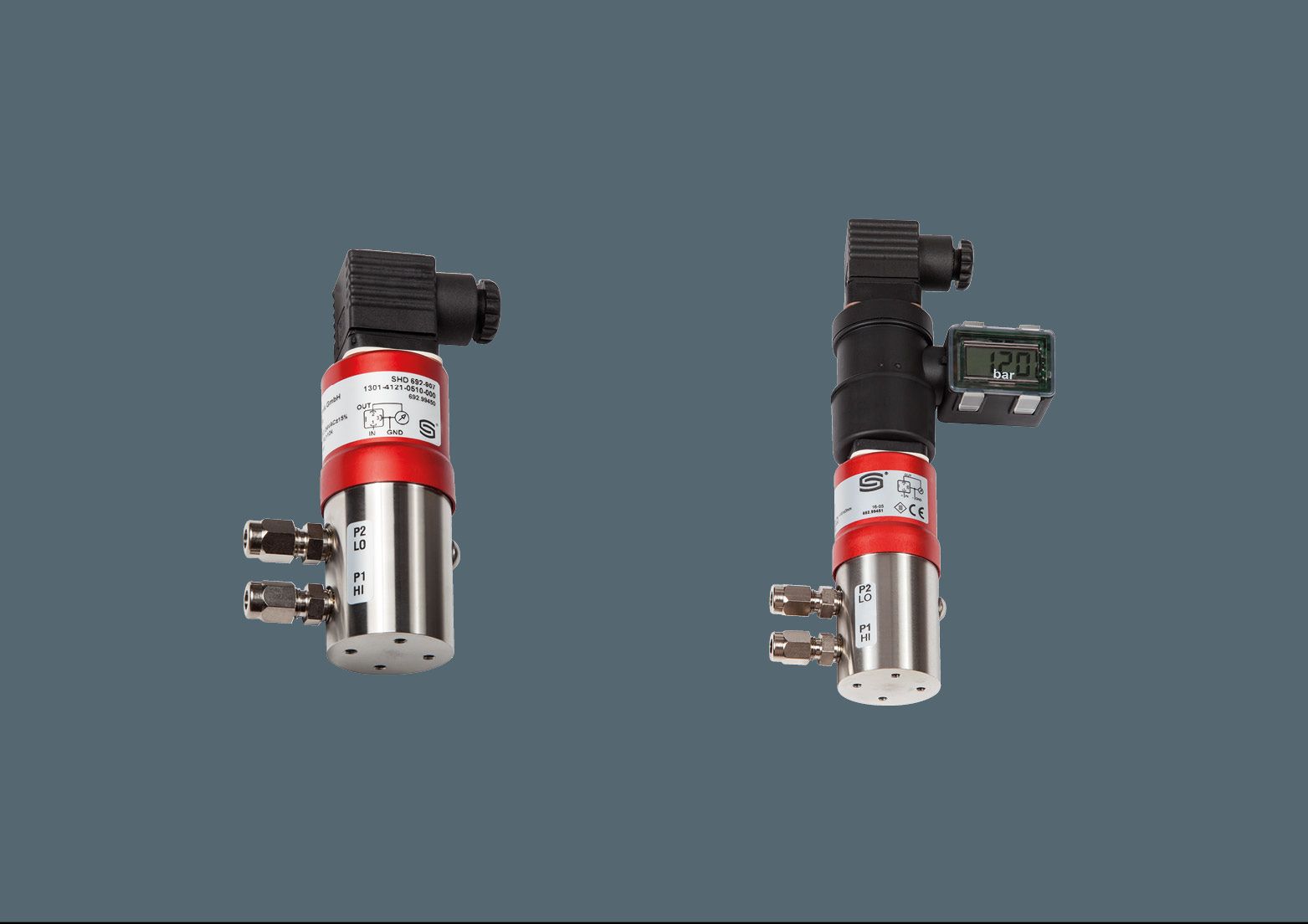
S+S Portfolio:
Differential pressure transducer
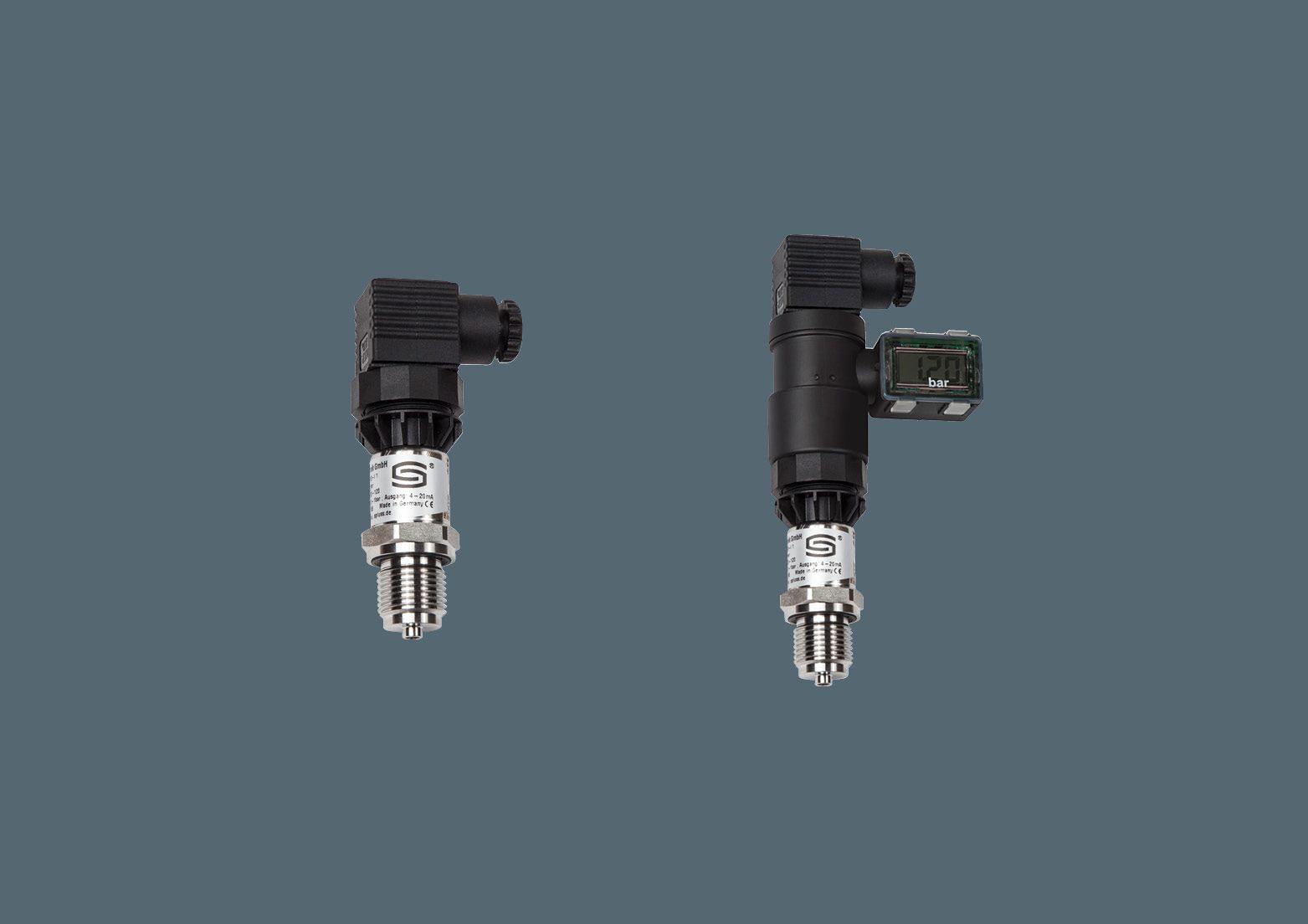
S+S Portfolio:
Relative pressure transducer
Where can I use differential pressure transducers?
- Building automation
- Filter cleanness status
- Piping
- Hydraulic systems
- Pneumatics
- Mechanical and plant engineering
What is a differential pressure transducer?
A differential pressure transducer is a type of pressure sensor or transducer designed to measure the difference in pressure between two points in a fluid or gas system. It converts the applied pressure difference into an electrical signal that can be used for monitoring, control, or data acquisition purposes.
How does a differential pressure transducer work?
A differential pressure transmitter measures the difference in pressure between two points in a fluid or gas system. It consists of three main components: a pressure-sensing element, a signal-conditioning circuit, and an output circuit.
Here's a simplified explanation of how a differential pressure transmitter works:
- Pressure-Sensing Element: Like in a differential pressure transmitter, the pressure-sensing element of a differential pressure transducer detects the pressure difference between two points in the system. It typically employs diaphragms, strain gauges, or other sensing technologies that deflect in response to the applied pressure.
- Deflection and Force Balance: The pressure-sensing element deflects in proportion to the differential pressure, creating a force imbalance. This deflection is used to convert the mechanical pressure into an electrical signal.
- Signal Conditioning: The electrical signal generated by the pressure-sensing element is conditioned using signal-conditioning circuitry. This circuitry may include amplifiers, filters, linearization techniques, and other components to enhance the accuracy, stability, and linearity of the signal.
- Output Circuit: The conditioned electrical signal is converted into a standardized output signal, such as 4-20 mA current or a 0-10 V voltage signal, which can be easily transmitted to a control system, data acquisition device, or display. The output signal represents the measured differential pressure.
- Calibration and Adjustment: Similar to a differential pressure transmitter, a differential pressure transducer is calibrated to ensure accurate measurement. Calibration involves adjusting the transducer's output to correspond accurately with known pressure differentials. Some transducers may have calibration options or adjustment mechanisms to fine-tune the output.
By measuring the differential pressure and converting it into an electrical signal, the differential pressure transmitter provides a reliable and proportional representation of the pressure difference between the two points in the system. This information is crucial for monitoring, control, and automation of various processes in industries ranging from HVAC to manufacturing.
What types of measured pressure are there?
There are several types of measured pressure commonly encountered in various applications.
The most common ones are differential pressure, relative pressure (also known as gauge pressure) and absolute pressure.
Understanding the specific type of pressure being measured is essential for selecting the appropriate pressure sensor or transducer and interpreting pressure readings accurately. Below you will find the explanation of each mentioned pressure type.
What is the difference between differential pressure, relative pressure and absolute pressure?
The main difference between an absolute pressure transducer and a differential pressure transducer lies in the reference point against which the pressure is measured. The text and graphics below illustrate those differences. Within them P0 = vacuum pressure, P1 = atmospheric pressure and P = pressure (measured on the specific spot where you want to measure).
A differential pressure transducer, as the name suggests, measures the difference in pressure between two points in a fluid or gas system. It calculates the pressure differential by comparing the pressure at one point with the pressure at another point. It does not provide the absolute pressure value but focuses solely on the difference between the two pressures being measured.
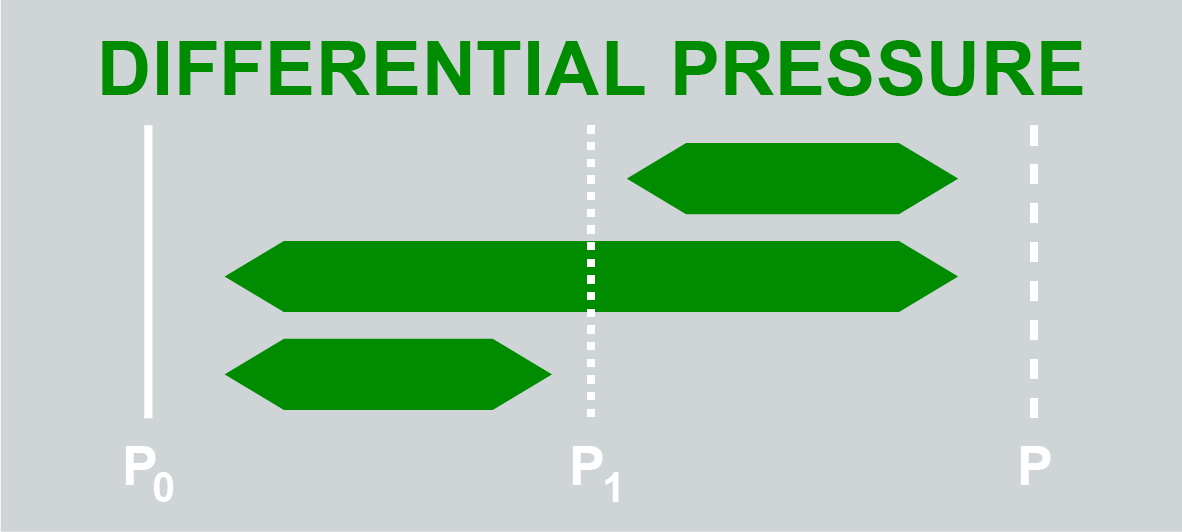
Relative pressure, also known as gauge pressure, is the measurement of pressure relative to the atmospheric pressure or a specified reference pressure. It represents the difference between the actual pressure and the reference pressure.
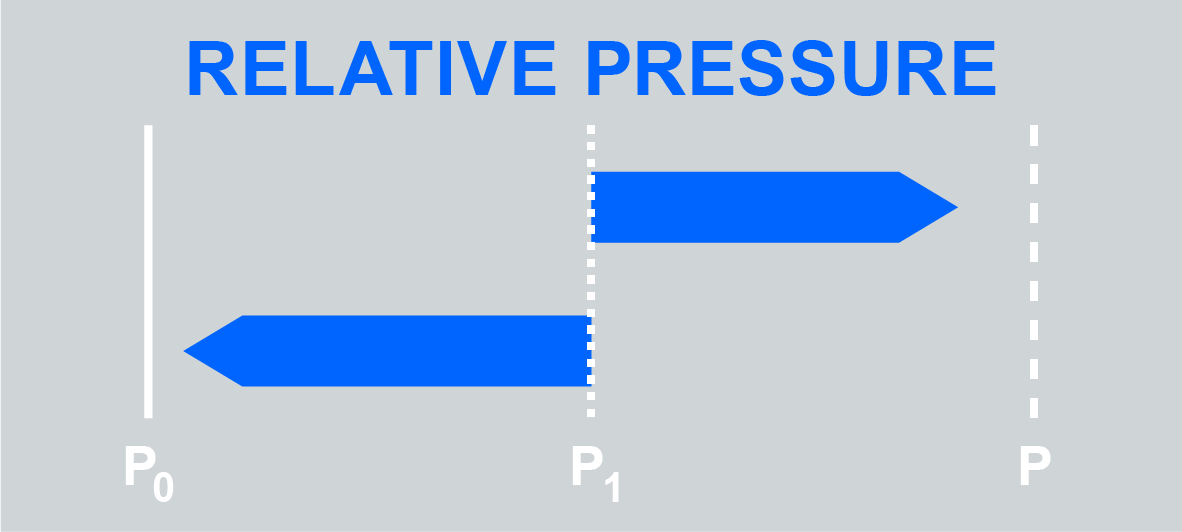
An absolute pressure transducer measures the pressure relative to an absolute vacuum or absolute zero pressure. It provides the absolute pressure value, which includes both the atmospheric pressure (or any other prevailing pressure) and the pressure being measured. In other words, it measures the total pressure exerted by a fluid or gas, regardless of any reference point.
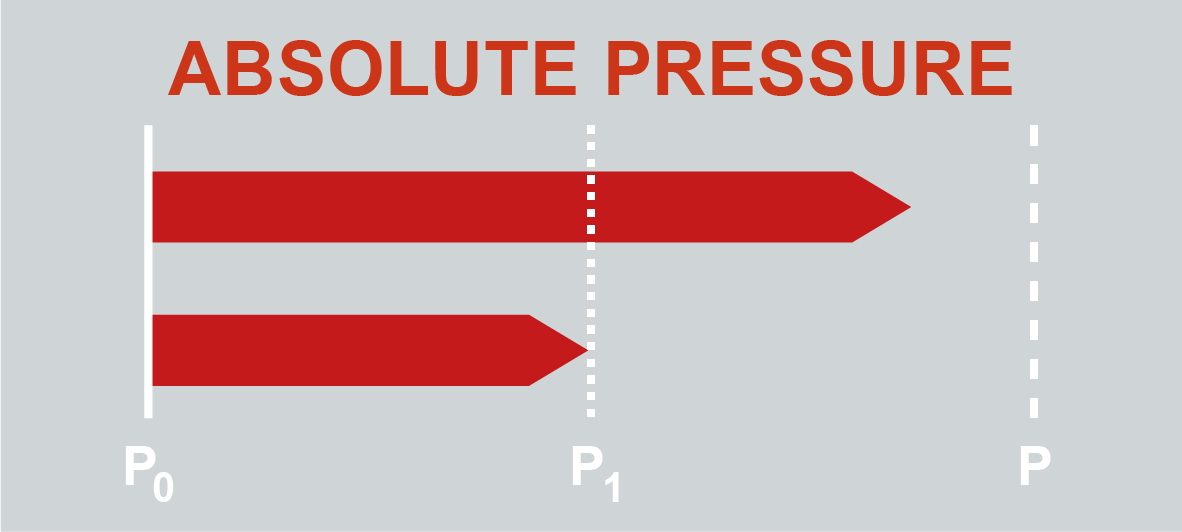
At S+S Regeltechnik GmbH, we take pride in offering top-quality differential pressure transducers that are designed to meet the demanding requirements of your applications. Our transducers provide reliable and accurate measurements, ensuring precise control and optimization.
With our differential pressure transducers, you can trust in their exceptional performance and durability. We offer a wide range of options, allowing you to choose the ideal transducer that fits your specific application needs. Whether you require transducers for building automation, HVAC, or within the process technology industry, we have you covered.
One of the key advantages of choosing S+S Regeltechnik is our commitment to providing cost-effective solutions without compromising on quality, as well as being a one-stop shop for all sensor/ field device related articles. We understand the importance of competitive pricing, and our differential pressure transducers offer exceptional value for their price. Our assortment exceeds the standard portfolio making it the perfect choice.
Explore our range of articles and product categories below to discover the versatility and reliability of our differential pressure transducers. Whether you are an HVAC contractor, building automation professional, or involved in the construction industry, we have the right solutions to enhance your systems and optimize indoor environments.
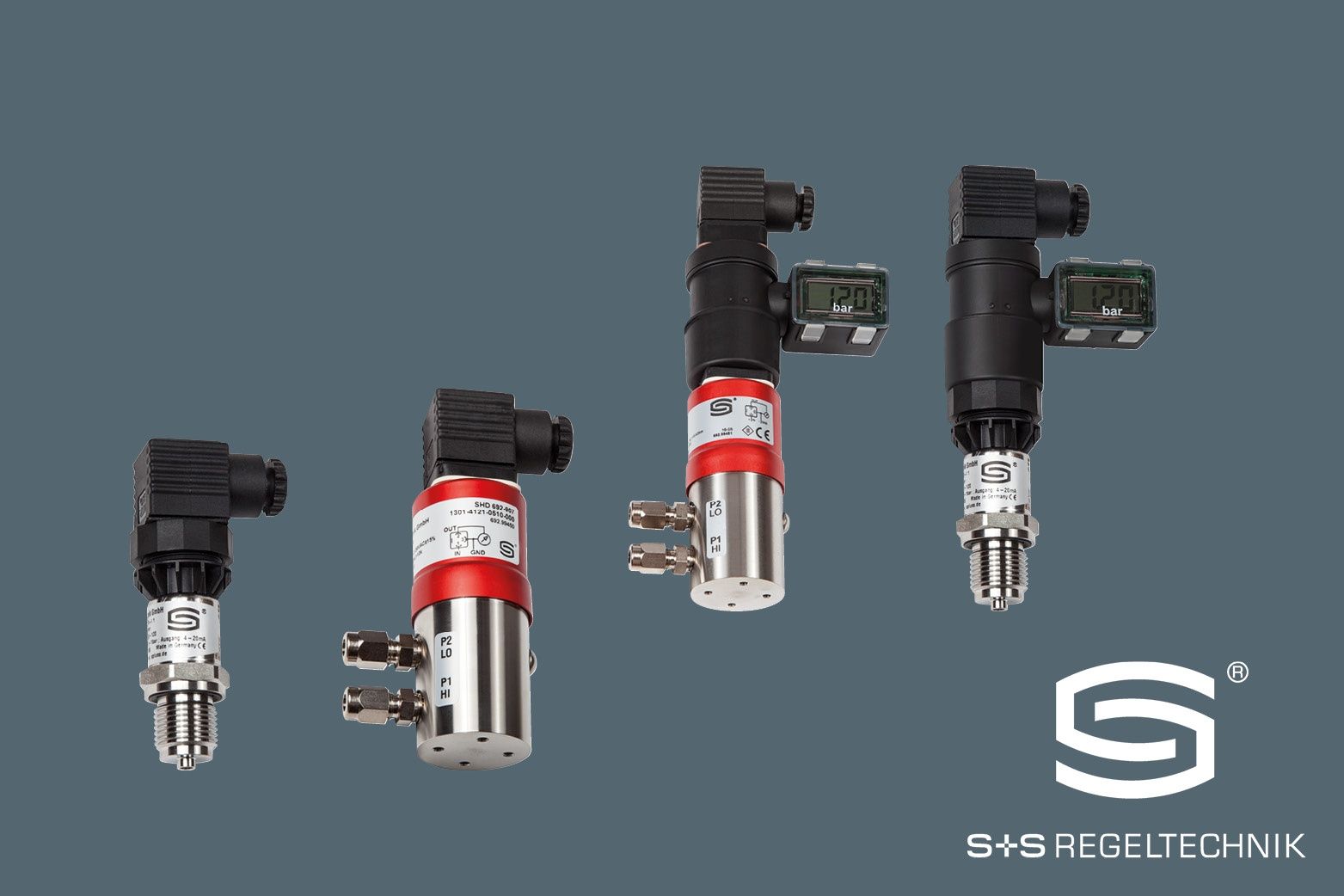
Differential pressure transducer
SHD 692
- Pressure type: differential
- Measuring ranges: 0..0,1 bar up to 0..10 bar
- Output: 0-10V or 4-20mA
- Measuring cell: ceramic
- Display: optional
- Connection: 2x G1/8"-27 NPT internal thread
Relative pressure transducer
SHD | SHD-SD
- Pressure type: relative
- Measuring ranges: 0..1 bar up to 0..40 bar
- Output: 0-10V or 4-20mA
- Measuring cell: steel or ceramic
- Display: optional
- Connection: G1/2" thread